
Flotation was carried out using a solids loading of 17 wt% at a pH of 8.3 – 8.5 till the froth was barren ( 1-1.5 minutes). Flotation conditions were kept unchanged for all the tests. The impeller power during conditioning was monitored using a dynamometer housed in the mixer.įlotation: A Denver D-2 flotation machine was used for flotation of 1 kg charge in a 5 liter float cell. The ratio of fatty acid to fuel oil were kept constant for all tests at 1:1 these values, were obtained from the flotation plants. The conditioning pH was maintained at 9.2 by addition of a known amount of modifier at the onset of conditioning. A four blade cruciform impeller (pitch = 45°) was used for mixing and the off-bottom clearance was kept at 0.25 inch (0.006 m). Materials and MethodsĬonditioning: Conditioning was done in a 1.75 liter stainless steel cell using a Ljghtnin Labmaster mixer. The extent of collector adsorption onto the phosphate particles depends on the conditioning variables such as the solids loading and the agitation speed which govern the degree of mixing achieved during the process. Often the improvement in flotation performance is sought by an increase in collector dosage. The conditioning efficiency is decided by the collector consumption and the phosphate recovery upon flotation.
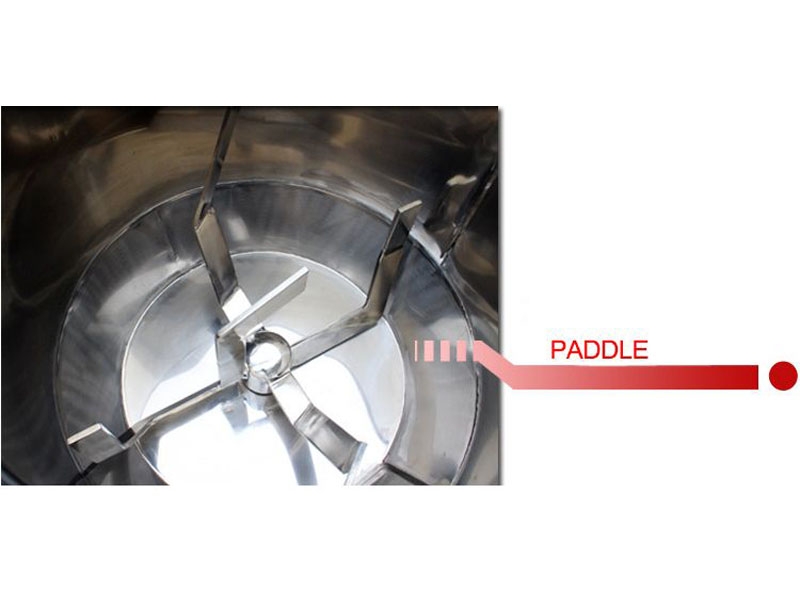
The flotation performance of phosphate ore in the anionic flotation stage is determined to a large extent by anionic conditioning, the unit operation prior to flotation where the reagents (collector) and phosphate slurry are mixed together. The process design emphasizes maximum recovery of phosphates in the anionic flotation stage to eliminate further processing of the underflow. Correlation of mixing with flotation recovery.

Minimum power requirements for complete suspension of slurries.Optimising Mixing in Anionic Conditioning Phosphates
